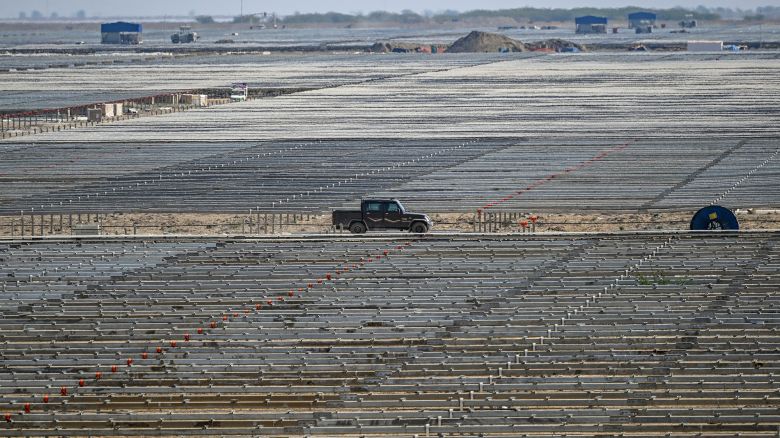
A coal billionaire is building the world’s biggest clean energy plant and it’s five times the size of Paris
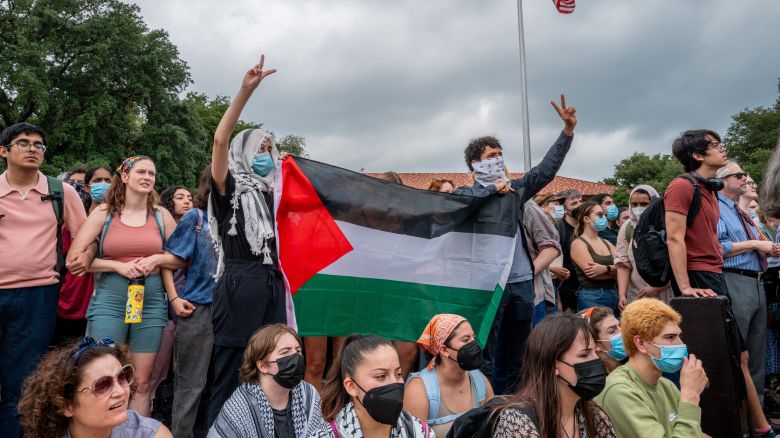
As pro-Palestinian protests sweep campus, student journalists are rushing to the big story and exams
What to Watch
Ad Feedback
In Case You Missed It
Ad Feedback
Ad Feedback