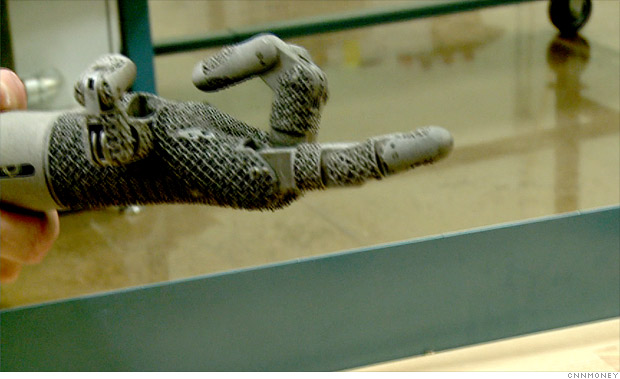
A robotic arm is among the creations Oak Ridge's scientists have manufactured with their cutting-edge 3D technology.
At the Oak Ridge National Laboratory in Tennessee, a group of scientists and engineers are experimenting with the future of manufacturing. They're making lighter, sturdier products in a fraction of the time usually required, and expanding the boundaries of what we can fabricate.
The process they're using is called additive manufacturing. It's essentially 3D printing using metals, plastics, and other building materials. Products are built one layer at a time. For instance, a layer of titanium dust is sprayed on a platform, then specific dust particles get zapped and melted with electron beams. The rest of the dust is blown off, and the next layer gets built.
The process allows manufacturers to build structures within structures, complex prosthetics, lighter airplane parts, and mesh metal structures that couldn't previously be constructed.
There are limitations, including the tremendous upfront cost of the machinery needed to do additive manufacturing -- each electron beam cabinet costs several million dollars.
It's currently limited to smallish items, and the technology doesn't yet exist to mix materials like plastic and metal. But Oak Ridge engineers think the technology will improve in the next few years to the point where additive manufacturing could be done on a much larger scale, and for a lot cheaper.
One day, an airplane could be built from the bottom up in a hanger. -David Goldman
NEXT: 3D TV -- no glasses required